Connecting Rod Manufacturer: Excellence in Diesel Engine Parts
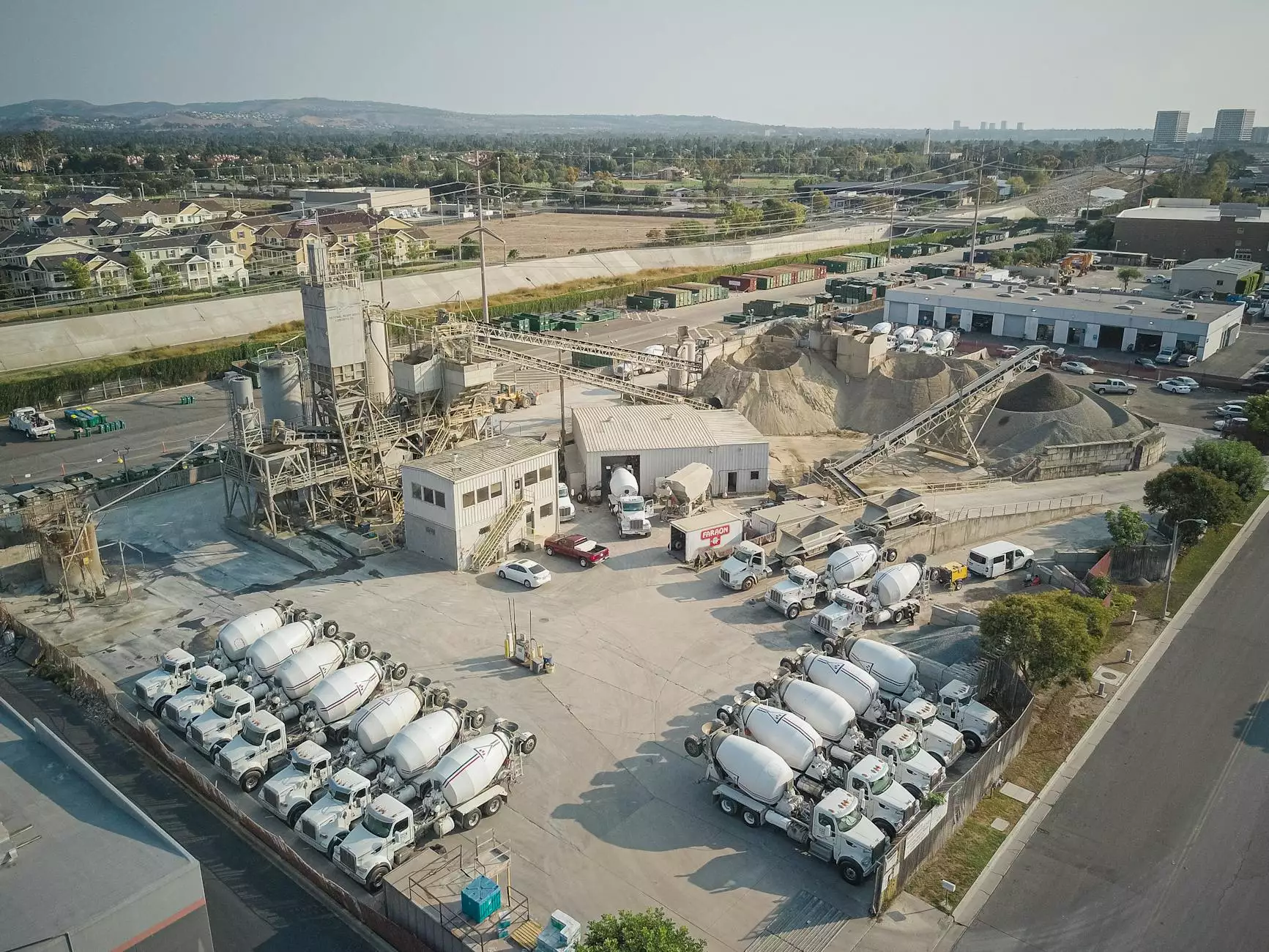
The connecting rod manufacturer industry plays a vital role in the automotive and machinery sectors, particularly for diesel engines. Connecting rods, as critical components, link the piston and the crankshaft, converting the linear motion of the piston into rotational motion.
The Importance of Connecting Rods in Diesel Engines
Connecting rods serve not merely as links; they bear significantly heavy loads during the engine's operation. Here are several reasons why they are essential:
- Load Bearing: The connecting rod must withstand high tensile strength and pressure. It faces extreme conditions such as temperature fluctuations and rapid motion.
- Durability: A high-performing connecting rod should possess a long operational life, minimizing the risk of failures that can lead to costly repairs.
- Efficiency: Properly engineered connecting rods contribute to the overall efficiency of the engine by optimizing performance and reducing emissions.
Understanding the Manufacturing Process
The overall quality of connecting rods is heavily influenced by their manufacturing process. A responsible connecting rod manufacturer employs advanced techniques and state-of-the-art technology. Below are essential steps involved in the manufacturing process:
1. Material Selection
Choosing the right materials is crucial. Common materials used in the production of connecting rods include:
- Alloy Steel: Known for its tensile strength, alloy steel is the most preferred material for connecting rods.
- Aluminum Alloys: Lightweight and resistant to corrosion, aluminum alloys are increasingly popular in performance-oriented applications.
2. Forging
Many quality connecting rods are made through the forging process. This involves:
- Heating: The material is heated to a high temperature to make it malleable.
- Shaping: The heated metal is then shaped using hammers or presses to achieve the desired form.
- Cooling: The forged components are cooled, enhancing their strength and integrity.
3. Machining
After forging, the connecting rods undergo precise machining to ensure accurate dimensions. This step includes:
- Drilling: Holes for bolts are precisely drilled to allow easy assembly with other engine components.
- Grinding: Eddie or honing techniques are used to create smooth surfaces necessary for performance.
4. Quality Control
Every reputable connecting rod manufacturer must implement rigorous quality control measures:
- Testing: Load testing and fatigue testing are performed to guarantee that each connecting rod meets industry standards.
- Inspection: Visual inspections and dimensional checks ensure that all products are free of defects.
Innovative Technologies in Connecting Rod Manufacturing
The landscape of manufacturing is constantly evolving, and modern connecting rod manufacturers are leveraging cutting-edge technology to enhance product quality and production efficiency. Here are some key innovations:
1. Computer Numerical Control (CNC) Machining
CNC machines provide unparalleled precision in milling and turning connecting rods. Advantages include:
- Precision: High dimensional accuracy leads to better engine performance.
- Reduction in Waste: CNC minimizes material waste due to its accuracy.
2. 3D Printing
Though still emerging in mass production, 3D printing can be beneficial for creating prototype connecting rods quickly. The benefits include:
- Speed: Rapid prototyping allows manufacturers to test designs quicker.
- Customization: Easily adjustable designs can cater to specific customer needs.
3. Material Science Advancements
Research in material sciences continuously yields new, stronger materials that can enhance performance while reducing weight, such as:
- Carbon Fiber Reinforced Polymers: Promising materials for high-performance and lightweight applications.
- Nano-structured Alloys: Offering superior strength-to-weight ratios.
Why Choose a Reliable Connecting Rod Manufacturer?
If you're in search of connecting rods, choosing a reputable manufacturer is paramount. Here are several factors to consider:
- Experience: A manufacturer with years of experience likely possesses the know-how to produce quality products.
- Reputation: Look at customer reviews and testimonials to gauge the reliability of the manufacturer.
- Certifications: Check for industry certifications that validate the manufacturer's adherence to quality standards.
- Customer Service: Knowledgeable and responsive support can significantly enhance your purchasing experience.
Sourcing Spare Parts from Clients
At client-diesel.com, we pride ourselves on being among the foremost spare parts suppliers for diesel engine components. Here’s why collaborating with us can be beneficial:
1. Comprehensive Inventory
Our extensive catalog includes a variety of connecting rods, engine components, and even rare parts. Whether you need replacements or performance upgrades, we have the parts you require.
2. Expert Consultation
Our team consists of industry experts who can advise you on the best choices for your specific needs. We understand the importance of optimizing your engine's performance and provide tailored guidance.
3. Quality Assurance
We stand behind our products. Each connecting rod goes through rigorous quality checks and testing to ensure reliability before it ever reaches your shop or garage.
Conclusion
As a leading connecting rod manufacturer, we embrace innovation, quality, and exceptional customer service. Whether you are involved in automotive repair, industrial machinery, or high-performance vehicles, the connecting rods from client-diesel.com will enhance your operations.
Investing in high-quality connecting rods is not just about buying a component; it’s about ensuring the long-term success of your engine's performance. Contact us today to explore our offerings and witness our commitment to excellence in the diesel engine parts industry.