The Profound Impact of Metal Die Casting in Modern Manufacturing
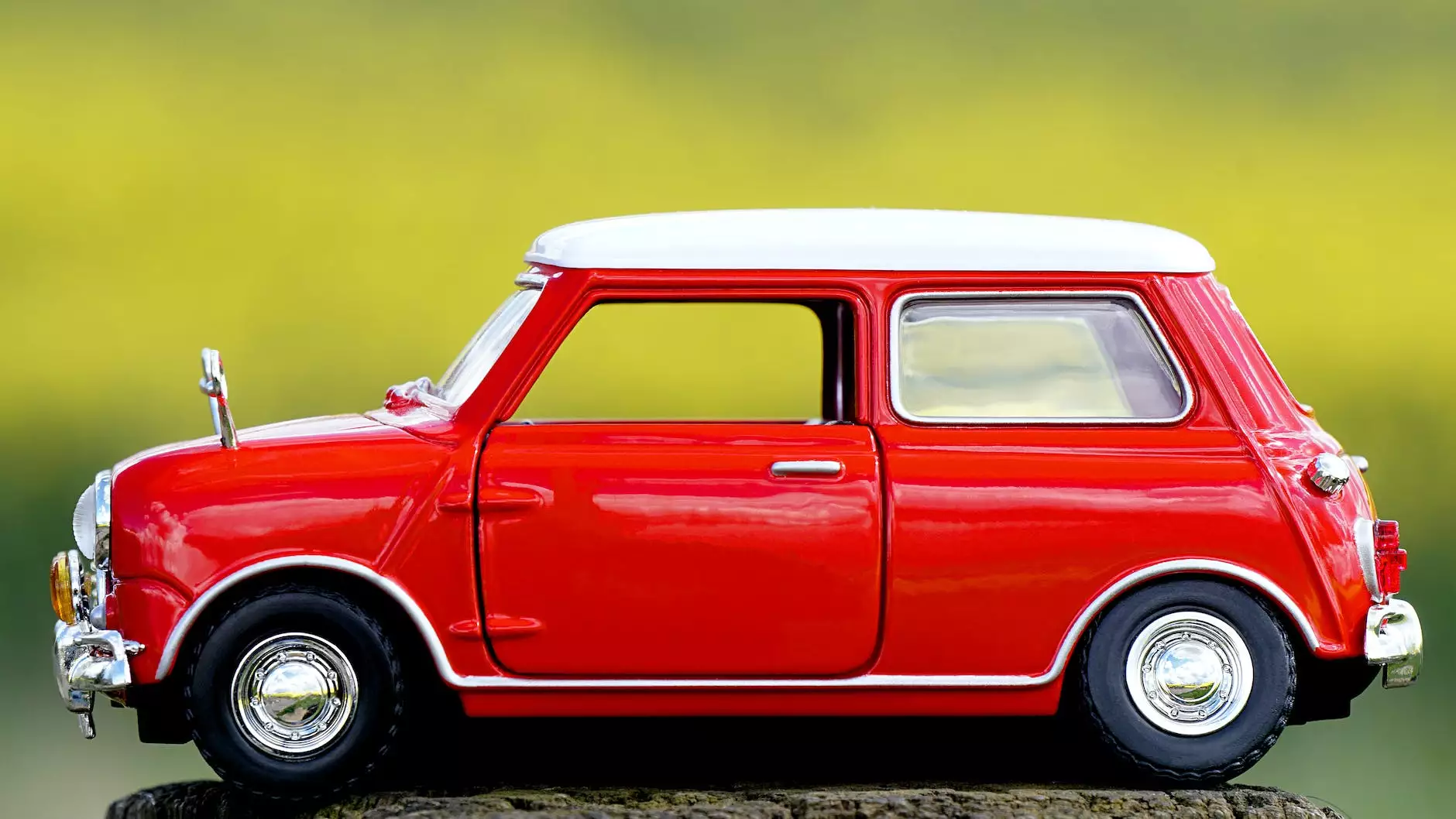
Metal die casting has emerged as a pivotal process in the world of manufacturing, revolutionizing the way components are produced across numerous industries. This article aims to delve deep into the intricacies of metal die casting, exploring its processes, advantages, applications, and how it contributes significantly to the business landscape while focusing on the prowess of Deep Mould in this domain.
What is Metal Die Casting?
Metal die casting is a manufacturing process in which molten metal is injected into a mold cavity under high pressure. This technique enables the production of high-quality metal parts with accurate dimensions and a smooth finish. Common metals used in die casting include aluminum, zinc, and magnesium due to their excellent fluidity and mechanical properties.
The Metal Die Casting Process
The process of metal die casting can be broken down into several key stages:
1. Mold Creation
The first stage involves creating a mold, specifically designed to produce the desired shape. Molds can be made from various materials, including steel, which is common for high-volume production, as it withstands high temperatures and pressures.
2. Melting the Metal
The metal is then melted in a furnace. The choice of metal depends on the application, with aluminum being favored for its lightweight and strength, while zinc offers excellent machinability and corrosion resistance.
3. Injection of Molten Metal
The molten metal is injected into the mold under high pressure, which ensures that it fills every contour of the mold. This stage is crucial as it determines the final quality of the cast component.
4. Cooling and Ejection
Once the molten metal has been injected, it is allowed to cool and solidify. After solidification, the mold is opened, and the casting is ejected. This rapid cooling process is critical in maintaining the integrity and dimensional accuracy of the component.
Advantages of Metal Die Casting
Metal die casting offers numerous advantages, making it a preferred choice in various industries:
- Precision and Quality: The process allows for high dimensional accuracy and fine surface finishes, reducing the need for additional machining.
- High Production Rates: Die casting is ideal for mass production, significantly increasing efficiency and lowering production costs.
- Material Utilization: The process ensures minimal waste, as excess metal can often be recycled.
- Complex Shapes: It enables the production of intricate shapes that might be challenging to achieve with other manufacturing processes.
- Improved Mechanical Properties: Die-cast components often exhibit superior mechanical properties due to the rapid cooling process.
Applications of Metal Die Casting
Given its versatility, metal die casting finds applications across a wide range of industries:
1. Automotive Industry
The automotive sector is one of the largest consumers of die casting. Components like engine blocks, transmission cases, and wheels benefit from the lightweight and durable nature of die-cast parts.
2. Electronics
In electronics, die casting is used for producing housings and heat sinks, which require both thermal conductivity and design intricacy.
3. Aerospace
The aerospace industry relies on die casting for producing critical components that must meet strict safety and durability standards.
4. Consumer Goods
From appliances to hand tools, die casting is prevalent in the consumer goods sector, providing cost-effective and high-quality products.
The Role of Deep Mould in Metal Die Casting
Deep Mould has positioned itself as a leader in the field of metal die casting by combining advanced technology with skilled craftsmanship. The company’s commitment to quality and precision ensures that every component produced meets the highest industry standards.
Advanced Technology and Techniques
Deep Mould employs state-of-the-art technology throughout the die casting process. This includes:
- Robust Mold Design: Utilizing CAD modeling for precise mold design.
- High-Performance Furnaces: Ensuring optimal melting conditions for consistent quality.
- Automated Injection Systems: For improved accuracy and efficiency in metal injection.
- Quality Control Measures: Rigorous testing and inspection protocols ensure that all products exceed customer expectations.
Customization to Meet Client Needs
One of the standout features of Deep Mould is its ability to customize solutions to fit the specific needs of clients. By offering tailored designs and rapid prototyping services, Deep Mould allows clients to bring their innovative ideas to life, ensuring a competitive edge in their respective markets.
Environmental Considerations in Metal Die Casting
As industries focus more on sustainability, metal die casting has adapted to meet environmental challenges. The recycling of metals, especially aluminum, plays a crucial role in minimizing waste and reducing carbon footprints. Deep Mould actively engages in sustainable practices, ensuring that the die casting process aligns with global environmental standards.
Challenges in Metal Die Casting
Despite its advantages, metal die casting does present some challenges, including:
- Initial Cost: The setup costs for die casting can be high, especially for custom molds.
- Material Limitations: Certain metals may not be suitable for die casting due to melting points or fluidity.
- Complexity in Design Changes: Once a mold is created, making alterations can be complicated and expensive.
Conclusion: The Future of Metal Die Casting
The future of metal die casting looks promising as technology continues to evolve. Innovations such as 3D printing for mold creation and improved alloy formulations are set to enhance the capabilities of die casting further. Companies like Deep Mould are leading the charge, adapting to changing market demands and pushing the boundaries of what is possible in manufacturing.
In conclusion, understanding the nuances of metal die casting and recognizing the contributions of leaders in this field, like Deep Mould, empowers businesses to make informed choices about their manufacturing processes. The blend of expertise and innovation in metal die casting not only enhances production efficiency but also ensures that companies remain competitive in an ever-evolving marketplace.