The Future of Manufacturing: Precision Injection Molded Components
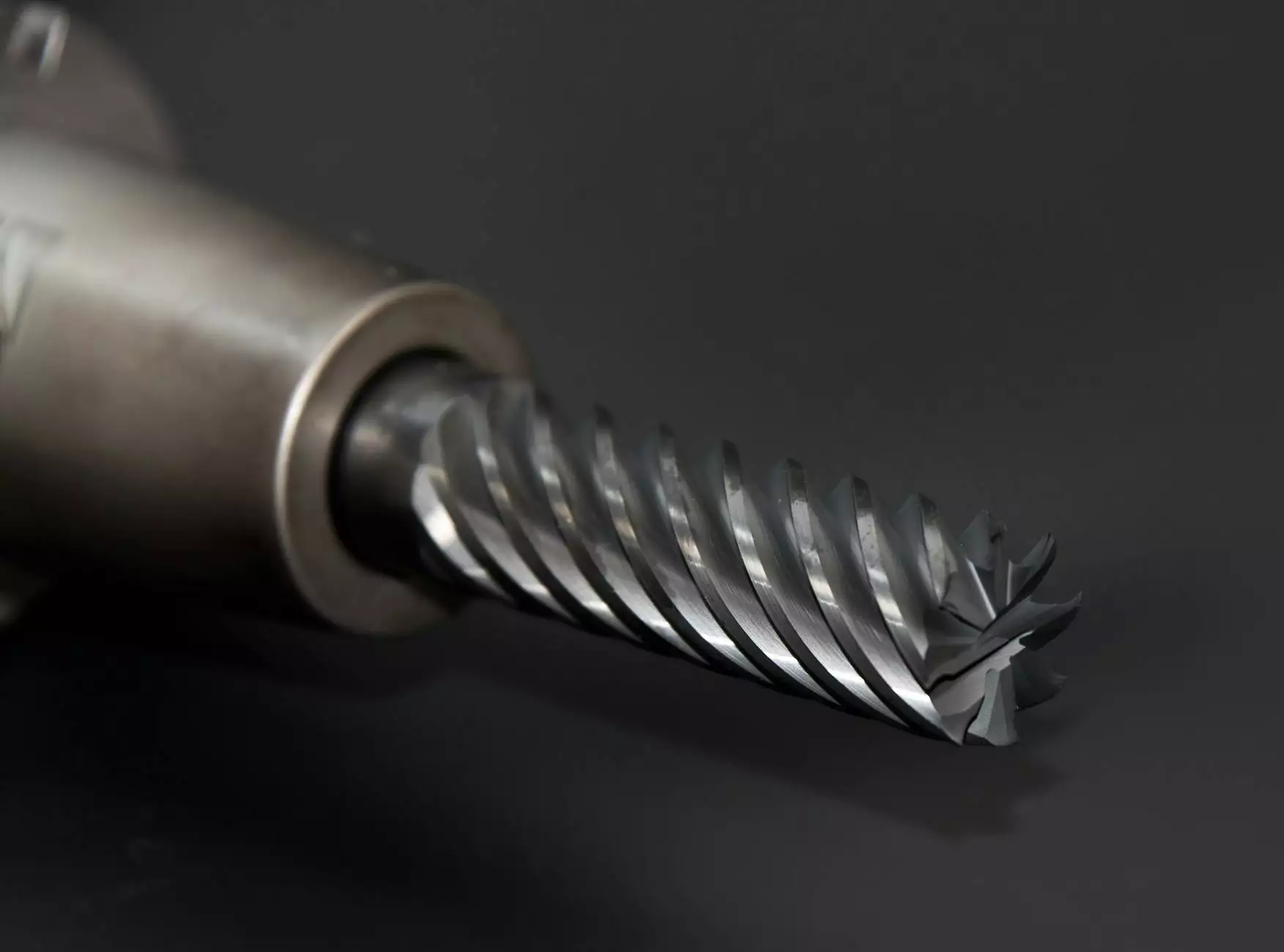
The manufacturing industry is continuously evolving, driven by technological advancements and the demand for high-quality components. One of the most significant innovations in this sector is precision injection molded components. This process has transformed the way products are made, offering enhancements in efficiency, accuracy, and sustainability.
Understanding Precision Injection Molding
Precision injection molding is a manufacturing process used to produce parts in large volumes with exceptional accuracy. It involves injecting molten material into a mold cavity, where it solidifies to form the desired shape. This process is particularly advantageous for creating intricate designs and complex geometries that are difficult to achieve with traditional manufacturing methods.
How Precision Injection Molding Works
The precision injection molding process can be broken down into several key steps:
- Material Selection: The first step involves selecting the appropriate materials, typically thermoplastics, thermosets, or elastomers, that can withstand the intended use.
- Mold Design: Next, molds are designed using sophisticated CAD software to ensure they meet the precision requirements of the final product.
- Injection Process: Molten material is injected into the mold under high pressure, ensuring that every cavity is filled accurately.
- Cooling: The material is allowed to cool and solidify within the mold. This stage is crucial for maintaining the shape and durability of the component.
- Demolding: Finally, the mold is opened, and the finished product is removed for further processing or delivery.
The Advantages of Precision Injection Molding
The benefits of using precision injection molded parts in manufacturing are numerous and impactful:
1. High Tolerance Levels
One of the most critical advantages of precision injection molding is the ability to achieve very tight tolerances. This is essential in industries where components must fit together seamlessly, such as in the automotive or aerospace sectors.
2. Cost-Effectiveness
Although the initial setup costs for creating molds can be high, the long-term savings achieved through mass production can significantly reduce per-unit costs. This makes precision injection molded components especially attractive for large-scale manufacturing.
3. Complex Geometries
The precision injection molding process allows for intricate designs which can be challenging to produce using traditional manufacturing methods. Complex features can be incorporated directly into the component, reducing the need for additional assembly steps.
4. Materials Versatility
A wide range of materials can be used in precision injection molding, including various plastics, metals, and composites. This versatility opens up possibilities for different applications and industries, from electronics to medical devices.
5. Low Waste Production
The precision of the molding process means that there is minimal waste of raw materials. This efficiency not only diminishes production costs but also aligns with sustainability practices by reducing the environmental impact.
Applications of Precision Injection Molding in Various Industries
The versatility and efficiency of precision injection molded components have made them vital in numerous applications across various industries:
1. Automotive Industry
In the automotive realm, precision-molded parts are used extensively for components such as dashboard elements, bezels, and even engine covers. These parts require high strength, low weight, and intricate designs, all of which are achievable through precision injection molding.
2. Electronics
Precision molded parts also play a crucial role in the electronics industry. Components such as housings, connectors, and insulators are produced using this method, ensuring that the products meet stringent safety and performance standards.
3. Medical Devices
The medical field demands high levels of precision and reliability, making precision injection molded components ideal for devices and instruments such as syringes, surgical tools, and diagnostic equipment. Compliance with regulatory standards is also a benefit of using this manufacturing process.
4. Consumer Products
In the consumer products market, the appeal of customized, intricate design can be realized through precision injection molding. From kitchenware to personal electronics, this approach allows businesses to innovate and meet consumer demands effectively.
5. Aerospace
The aerospace industry benefits from precision injection molded parts due to their lightweight nature, which enhances fuel efficiency. Components such as housing, interior fittings, and structural elements are often created using this technology.
Challenges in Precision Injection Molding
While there are numerous benefits to utilizing precision injection molding, it is essential to be aware of the challenges that may arise:
1. High Initial Investment
The design and production of molds can incur significant upfront costs, making it somewhat less accessible for small-scale manufacturers.
2. Complexity in Design
Designing molds for precision injection molded parts requires advanced engineering knowledge and sometimes complex CAD software, which can be a barrier for inexperienced manufacturers.
3. Production Limitations for Low Volumes
For low-volume production runs, the costs associated with mold production often outweigh the benefits, making it less favorable compared to alternative manufacturing methods.
Choosing the Right Fabrication Partner
Selecting a proficient manufacturing partner is crucial when venturing into precision injection molding. Here are some factors to consider when choosing a partner:
- Experience and Expertise: Look for a company with a proven track record in precision injection molding and a deep understanding of your specific industry needs.
- Technology and Equipment: Ensure the facility is equipped with the latest technology and machinery to deliver high-quality, precise components.
- Quality Assurance Processes: Investigate their quality control measures to ensure that the products meet industry standards and your expectations.
- Flexibility and Scalability: A good partner should be able to accommodate your needs whether you require a small batch or large production runs.
- Customer Support: Effective communication and support throughout the entire process is essential for successful collaboration.
DeepMould.net: Leading the Way in Precision Injection Molding
At DeepMould.net, we are proud to be at the forefront of the precision injection molding revolution. Our commitment to quality, innovation, and sustainability sets us apart in the metal fabrication industry.
Our Services
We offer a comprehensive range of services, including:
- Custom Mold Design: Tailored solutions to meet specific needs.
- Prototype Development: Rapid prototyping to bring ideas to life.
- Production Runs: Scalable production to accommodate any volume.
- Post-Production Services: Additional finishing services for enhanced quality.
Our Commitment to Sustainability
We understand the importance of sustainable manufacturing practices. Our precision injection molded components are designed with environmental consciousness in mind, ensuring minimal waste and energy-efficient production processes.
Conclusion
The shift towards precision injection molded components is not just a trend; it's a fundamental evolution in the manufacturing landscape. Businesses that embrace this technology stand to benefit from increased efficiency, reduced costs, and the ability to innovate quickly. As a leader in this field, DeepMould.net is dedicated to providing high-quality solutions that meet the diverse needs of our clients across various industries. By harnessing the power of precision injection molding, we are paving the way for a future of manufacturing that is more precise, efficient, and sustainable.