The Ultimate Guide to Hydraulic Hose Connectors
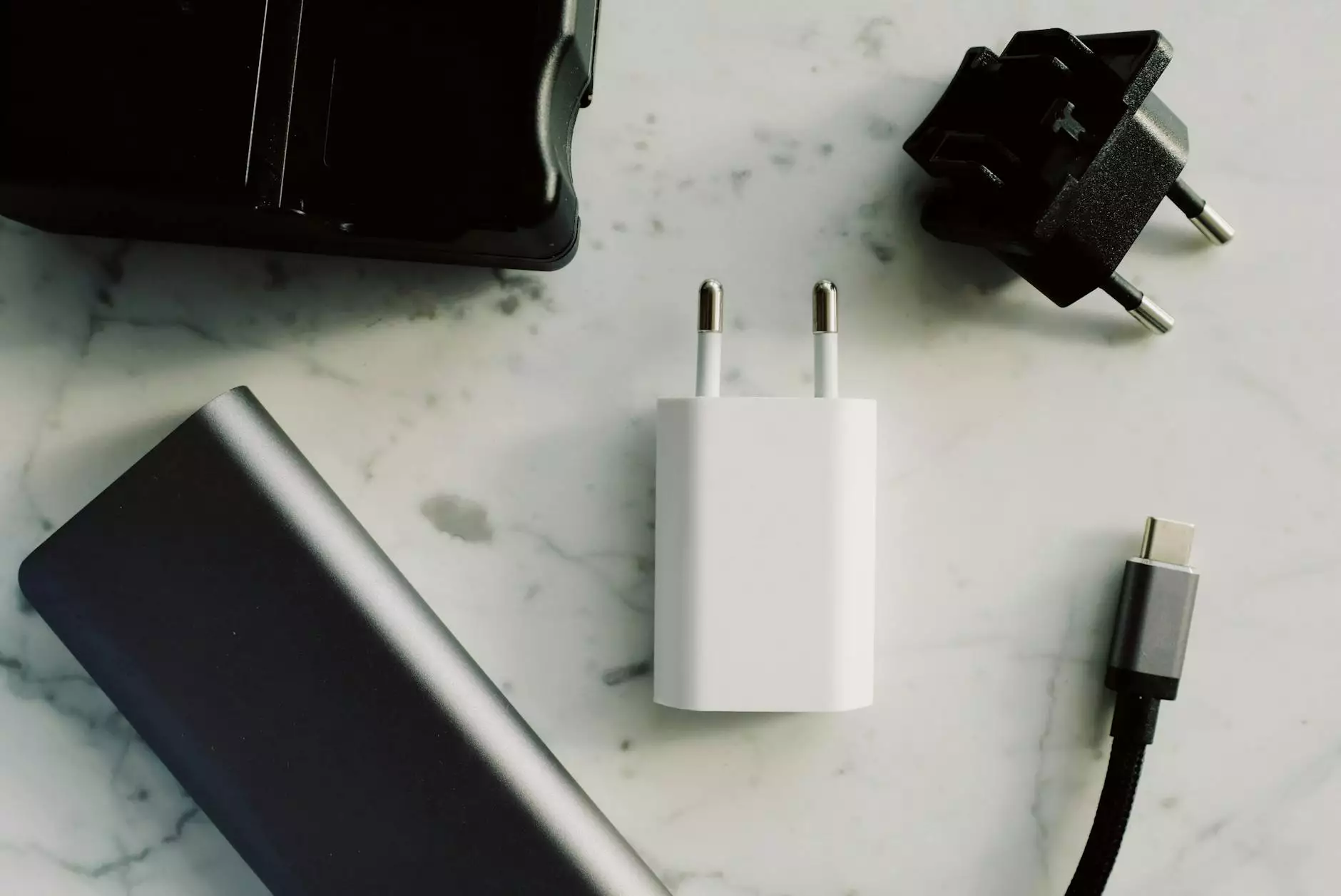
Hydraulic hose connectors play a crucial role in the functionality of hydraulic systems across various industries. These essential components ensure the safe and efficient transfer of hydraulic fluids, making them indispensable in heavy machinery, construction, automotive, and many other applications. In this comprehensive guide, we delve deep into the intricacies of hydraulic hose connectors, their types, applications, benefits, and how to choose the right ones for your needs.
Understanding Hydraulic Hose Connectors
At its core, a hydraulic hose connector is a fitting that connects hoses, pipes, or tubes in a hydraulic system. These connectors must endure high pressures and temperatures, providing leak-proof solutions to ensure optimal system performance. The quality of the connectors affects the overall efficiency, safety, and longevity of hydraulic systems.
Types of Hydraulic Hose Connectors
There are several types of hydraulic hose connectors designed to suit various applications. Each type has its unique features and advantages:
- Barbed Connectors: Commonly used in low-pressure applications, barbed connectors provide a reliable grip on the hose.
- Swivel Connectors: Ideal for applications where flexibility is needed, swivel connectors allow for rotation of the hose without twisting.
- Reducer Connectors: These connectors are used to connect hoses of different diameters, ensuring efficient fluid flow.
- Threaded Connectors: Available with various threading standards (NPT, BSP), these connectors provide robust sealing for high-pressure applications.
- Quick Couplers: Perfect for applications requiring frequent disconnects, quick couplers allow for easy connection and disconnection with minimal fluid loss.
Why are Hydraulic Hose Connectors Important?
Using high-quality hydraulic hose connectors is vital for several reasons:
1. Safety
Hydraulic systems operate under high pressure. A failure in any component, especially connectors, can result in catastrophic malfunctions. Quality connectors minimize the risk of leaks and explosions, ensuring a safe working environment.
2. Efficiency
Efficient fluid transfer is critical for hydraulic systems. Poor-quality connectors can lead to pressure drops and leaks, reducing overall system performance.
3. Cost-effectiveness
Investing in quality hydraulic hose connectors can prevent costly repairs and downtime, ultimately saving money in both the short and long term.
Key Applications of Hydraulic Hose Connectors
Hydraulic hose connectors are utilized in a wide range of industries:
1. Construction
In construction equipment like excavators and cranes, hydraulic connectors are essential for operating various functions such as lifting and excavation.
2. Automotive
In automotive industries, hydraulic systems are used for braking, steering, and transmission systems. Connectors ensure these systems function reliably.
3. Agriculture
Agricultural machinery relies on hydraulic systems for various tasks, from planting to harvesting. Quality connectors contribute to efficient operation.
4. Manufacturing
Manufacturing equipment often uses hydraulic systems for automation and control. Reliable connectors are a key component of these systems.
Choosing the Right Hydraulic Hose Connectors
Selecting the appropriate hydraulic hose connectors can significantly impact your hydraulic system's effectiveness. Here are some factors to consider:
1. Compatibility with Hoses
Ensure that the connectors are compatible with the hoses you are using. This includes checking the diameter, pressure ratings, and materials.
2. Pressure Rating
Every hydraulic system operates within specific pressure limits. Choose connectors that can withstand the maximum operating pressures of your system.
3. Material Selection
Connectors are commonly made from materials like steel, brass, or plastic. The choice of material should be based on the fluid being transported, environmental conditions, and durability requirements.
4. Assembly Method
Consider how the connectors will be assembled. Some connectors may require special tools or methods for installation, while others are designed for quick and easy assembly.
Maintenance Tips for Hydraulic Hose Connectors
To ensure the longevity and performance of your hydraulic hose connectors, consider the following maintenance tips:
1. Regular Inspection
Inspect connectors regularly for signs of wear, corrosion, or leaks. Early detection can prevent more significant issues later on.
2. Cleanliness
Keep connectors clean and free from contaminants. Dirt and debris can cause improper sealing and lead to leaks.
3. Proper Torque Specifications
Ensure that all connectors are tightened to the manufacturer’s torque specifications to maintain optimal sealing and pressure ratings.
4. Replace Worn Connectors
Don’t hesitate to replace connectors that show signs of damage or wear. Using worn connectors can increase the risk of leaks and reduce system efficiency.
Conclusion
In conclusion, hydraulic hose connectors are essential for the reliable and efficient operation of hydraulic systems across various industries. Selecting the right connectors, maintaining them properly, and understanding their applications can ensure safety, efficiency, and cost-effectiveness in your operations. For high-quality connectors suited to your needs, explore the range available at fitsch.cn.