Leading Silicone Injection Molding Machine Manufacturers
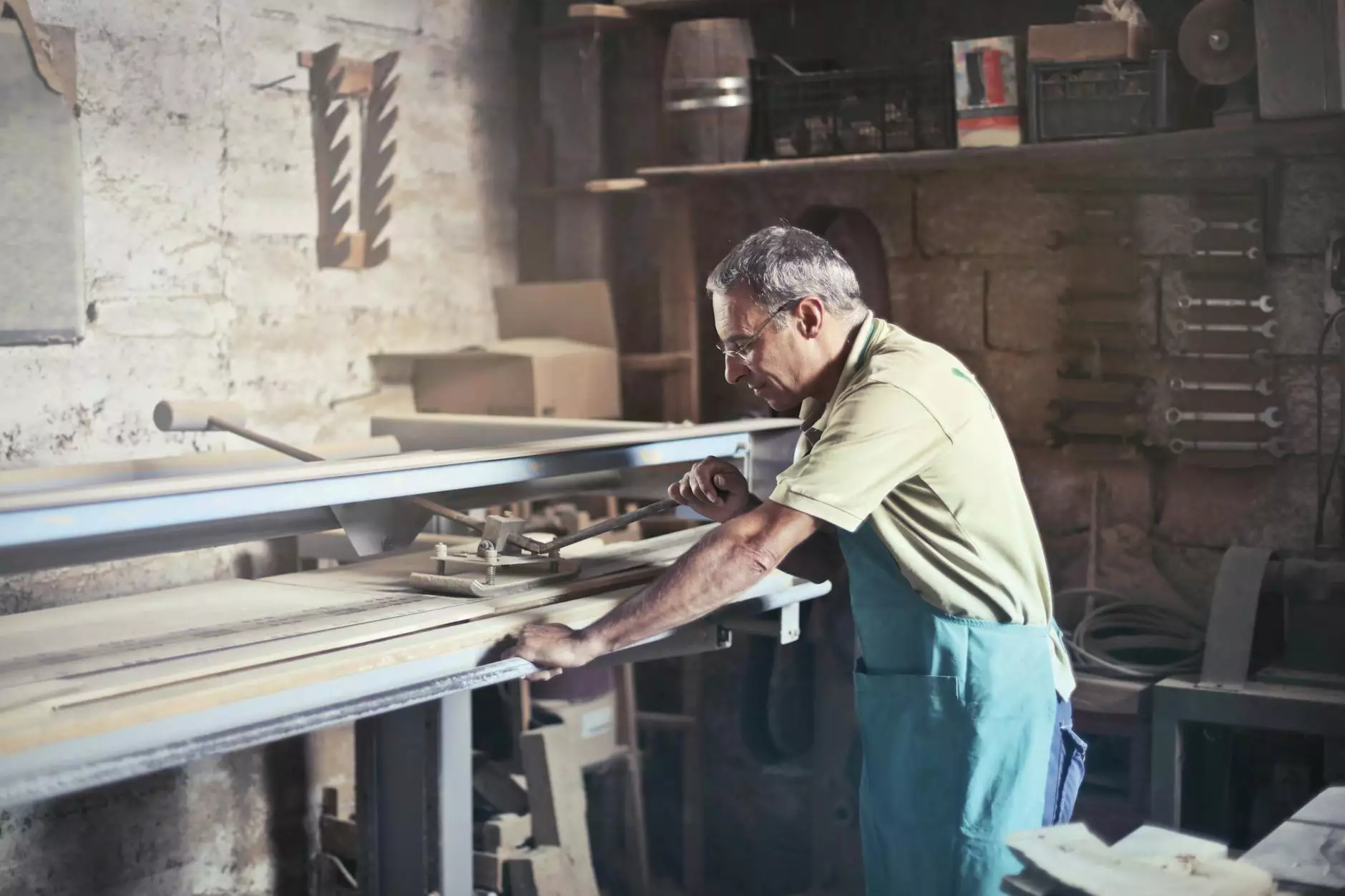
The silicone injection molding industry has witnessed significant growth over the years, driven by its critical applications in various sectors, particularly in electronics and medical supplies. As a result, the role of silicone injection molding machine manufacturers has become increasingly important. This article delves into the intricacies of the industry, highlighting the technological advancements, industry applications, equipment capabilities, and the leading manufacturers shaping the future of silicone injection molding.
Understanding Silicone Injection Molding
Silicone injection molding is a specialized manufacturing process that utilizes silicone materials to produce various parts and products with precise dimensions and remarkable properties. This method involves injecting liquid silicone rubber (LSR) into molds to create items that can withstand extreme temperatures, resist environmental degradation, and offer excellent insulating properties. The versatility of silicone makes this manufacturing process indispensable in numerous applications.
Applications of Silicone Injection Molding
Silicone injection molding caters to various sectors, notably:
- Electronics: Producing seals, gaskets, and housing for electronic devices that require durability and moisture resistance.
- Medical Supplies: Manufacturing components like syringes, catheters, and seals that must meet strict hygiene standards.
- Automotive Components: Offering parts that can tolerate high heat and resist wear.
- Consumer Goods: Creating innovative, flexible products like kitchenware and toys.
Key Advantages of Using Silicone Injection Molding
The shift towards silicone injection molding is fueled by several key advantages:
- Durability: Silicone materials are known for their long-lasting properties and ability to withstand physical stress.
- Temperature Resistance: Silicone can endure a wide range of temperatures without losing integrity, making it ideal for multiple applications.
- Biocompatibility: Particularly important in the medical field, silicone is non-toxic and can be safely used in products that come into contact with the human body.
- Flexibility and Versatility: Silicone can be molded into various shapes and forms, allowing for creativity and innovation in product design.
Technological Advancements in Silicone Injection Molding
As the demand for precision and efficiency increases, silicone injection molding machine manufacturers are continually innovating. Companies are integrating advanced technologies such as:
- Robotics and Automation: Streamlining the production process, reducing labor costs, and increasing accuracy.
- Industry 4.0 Solutions: Implementing IoT technologies for real-time monitoring and data analytics to optimize production efficiency.
- Advanced Mold Design Techniques: Innovative molds ensure superior product quality and reduced cycle times.
Leading Silicone Injection Molding Machine Manufacturers
The following are some of the leading manufacturers renowned for their cutting-edge silicone injection molding machines:
Nolato
Nolato stands at the forefront of silicone injection molding, providing optimal solutions for the electronics and medical supplies industries. Their machines are designed for precision, efficiency, and adaptability to meet diverse product demands.
Wabash MPI
Wabash MPI specializes in creating high-quality silicone injection molding machines that excel in performance and longevity. Their commitment to innovation and customer service makes them a trusted partner in the manufacturing sector.
Haitian International
As one of the largest manufacturers of injection molding machines, Haitian International offers advanced solutions tailored for silicone applications, ensuring high productivity and cost-effectiveness.
The Future of Silicone Injection Molding
The future of silicone injection molding appears bright, with evolving technology and expanding applications. As more industries recognize the advantages of silicone, manufacturers are likely to enhance their operational capacities and innovate further.
Market Trends Driving Growth
Several market trends are influencing the growth of silicone injection molding:
- Increasing Demand for Medical Supplies: The ongoing need for medical devices and supplies, especially post-pandemic, is driving innovation in silicone manufacturing.
- Growth in Consumer Electronics: As electronics become more complex, the need for durable, flexible silicone products continues to rise.
- Sustainability Initiatives: Manufacturers are focusing on eco-friendly materials and sustainable production processes to meet regulatory standards and consumer demand.
Best Practices for Selecting a Silicone Injection Molding Machine Manufacturer
When choosing a silicone injection molding machine manufacturer, consider the following best practices:
- Evaluate Technical Expertise: Ensure the manufacturer has a proven track record and expertise in silicone injection molding.
- Check Equipment Capabilities: Assess whether their machines can handle your specific production requirements, including size, volume, and complexity.
- Consider After-Sales Support: A reliable manufacturer should offer comprehensive support, including maintenance, training, and troubleshooting.
- Request Client References: Feedback from previous clients can provide valuable insights into the manufacturer's reliability and product quality.
Conclusion
In conclusion, the realm of silicone injection molding machine manufacturers is pivotal to the success of industries reliant on innovative and reliable silicone products, especially in electronics and medical supplies. Embrace the opportunities that this evolving field presents and consider partnering with reputable manufacturers like Nolato to drive business growth and innovation.
By staying informed and adapting to the rapid changes in technology and market demands, your business can not only survive but thrive in this competitive landscape.